A guide to the practical considerations of calibrating weighing instruments is presented here
Throughout the chemical process industries (CPI), weighing instruments find a range of important uses and are often a critical piece of equipment for many processes. Monitoring feed rates of raw materials by weight, ensuring that exact amounts of chemicals enter final product formulations, dispensing materials for packaging and conducting research and development work all depend on accurate and consistent weighing of materials. Weighing instruments with high accuracy are positively associated with good product quality control, through meeting industry standards; reduced downtime, by maintaining continuous operations; and good environmental compliance, through avoidance of overfilling and spills.Various types of scales and balances are used for a range of operations across the CPI, including the following: analytical balances for extremely precise measurement; precision balances for weighing chemicals with tight tolerances; industrial scales for heavy loads in bulk chemical production; and hazardous area scales in potentially explosive environments (Figure 1).

To maintain accuracy and ensure valid measurement results, weighing instruments should be calibrated regularly. A proper, metrologically traceable calibration is the only way to know how accurately weighing instruments are measuring. Some weighing instruments are used for legal measurements or measurements used as basis for monetary transfer. These are part of a legal or statutory verification program based on legislation. Often the calibration of weighing instruments is based on a quality system, such as ISO 9000 (standards for quality assurance in manufacturing; International Organization for Standardization; Geneva, Switzerland; ). There are dedicated regulations for weighing instruments and their calibration [1–3]. In this article, the main focus is on the practical considerations and required tests for calibrating weighing instruments.
Preparations before calibration
Proper calibration of weighing instruments requires some information gathering and special preparations before beginning, including assembling information about the technical characteristics of the weighing instrument — such as maximum weight, d value (ratio of scale capacity to increment size) and so on — as well as the accuracy requirements for the measurement (maximum error allowed and uncertainty). Also, those calibrating weighing instruments need a plan for adjusting the scale, if necessary. Typically, the entire measurement range of the instrument is calibrated during a calibration session and the calibration should be performed in the same location where the instrument will be used. Before beginning, ensure that there are sufficient calibration weights available for the calibration procedure. The weighing instrument should be switched on at least 30 minutes before starting the calibration. The temperature of the calibration weights should be stabilized to the same temperature as the area where the instrument is located. The weighing instrument should be level horizontally. This is especially true for small weighing instruments designed for high accuracy. Before starting calibration tests, perform a few pre-tests by placing weights close to the maximum of the measurement range onto the instrument to confirm that it working normally. In case the weighing instrument fails in calibration and it is adjusted, you should make an “as found” calibration before adjustment and an “as left” calibration after adjustment.Calibration tests
The following section outlines the different tests that should be undertaken as part of the weighing-instrument calibration (Figure 2).
Eccentricity test. During normal use of a weighing instrument, loads being weighed are not always located perfectly on the center of the load receptor. Sometimes the results of a weighing instrument can vary slightly depending on the exact placement of the load on the load receptor. In order to determine the extent of the effect that the location of the load has on the measurement results, the eccentricity test is performed.
In an eccentricity test, the reference load is placed in a few different specified locations on the surface of the load receptor. First, the load is placed in the center of the load receptor (the load’s center of gravity) and the weighing result is observed. Next, the load is placed in four different sectors of the load receptor offset from the center.The diagrams in Figure 3 show rectangular and round load receptors, but in practice, there may be many different shapes of load receptors, so the locations of the load can vary. Guidelines for load placement using alternatively shaped load receptors can be found in Standards OIML R76 and EN 45501 [3, 4].

Repeatability test. Like almost any instrument, weighing instruments may suffer from repeatability issues, which refer to variations in measurement results when the same load is measured multiple times. To assess the repeatability performance of a weighing instrument, a repeatability test is conducted (Figure 4).

Weighing test. The purpose of the weighing test is to check the accuracy (calibrate) of the weighing instrument throughout its whole range in several steps, with increasing and decreasing weight.
The most common for a weighing practice is the following: start by zeroing the instrument without any load. Set the loads of the first test point, wait for stabilization, then record the indication. Continue increasing the loads through all the increasing test points. Once the maximum load is recorded, start decreasing the loads through the decreasing test points. In some cases, the weighing instrument may be calibrated with increasing loads only or decreasing loads only. Typically, five to 10 different loads (test points) are used for this test. The heaviest load should be close to the maximum capacity of the instrument. The smallest test load can be 10% of the maximum load, or the smallest weight normally used. Generally, the test points are selected so that they are equally distributed throughout the range. More test points can be used within the typical usage range for the instrument. For multi-range instruments, each measurement range needs to be calibrated separately.Linearity
In a weighing test, using multiple points throughout the measurement range of the instrument helps to reveal issues with linearity. Linearity issues refer to those indicating that the instrument does not measure with equal accuracy throughout the measurement range. Even if the weighing results for zero and the full span are correct, there may be errors, termed linearity errors, in the middle part of the range. Figure 5 represents a general illustration of nonlinearity. The instrument’s zero and full range are adjusted correctly, but there is error in the midrange due to nonlinearity of the instrument.

Minimum weight test
The purpose of the minimum weight test is to find the smallest load that can be measured while still achieving reliable measurement results and fulfilling the accuracy requirements. When the measured value gets smaller, typically the relative error of the reading becomes higher. The weighing instrument should not be used to measure any loads smaller than the minimum load. Minimum weight tests are not always required, but are common in some industries, such as pharmaceutical manufacturing.Reference weights
When calibrating weighing instruments, it is recommended to use classified reference weights from metrological organizations such as NIST (U.S. National Institute of Standards and Technology; Gaithersburg, Md.; ) or OIML (Organisation Internationale de Métrologie Légale; Paris, France; ). Reference weights should be handled in such a way that it does not change the metrological characteristics of the weights. The weights should be kept off surfaces that could cause scratches and dirty surfaces that could introduce foreign materials. When cleaning weights, special attention should be paid to proper cleaning methods. Smaller reference weights should always be handled with gloves, rather than with bare hands, to avoid any depositing grease or dirt from fingers onto the weights. Touching only with gloved hands will also help avoid warming the weights to a higher temperature than the surrounding environment. When not in use, all reference weights should be stored in their own designated storage boxes. Weights should be stored so that only authorized personnel have access to them. Very large weights should be covered and stored in stable environmental conditions, where situations like moisture condensing on the weights’ surface, for example, are avoided. For reference weights, a distinction between nominal mass and conventional mass is made. Nominal mass is the designated mass of the given weight. When the weight is accurate enough, it is sufficient to use the nominal mass as the true value for legal verification. The conventional mass is the actual calibrated mass of the weight that has been corrected with any required local corrections. To make traceable calibrations, conventional mass should always be used. Reference weights should be traceably calibrated regularly using an accredited calibration laboratory or a national calibration laboratory. Typically, the calibration period for reference weights is 1 to 5 years.Factors affecting calibration
There are several factors to note that may have an affect on the calibration of weighing instruments — especially smaller and more sensitive devices.Local gravity. Gravity is slightly different in different locations around the globe. This is due to many factors, such as altitude (lower gravity at higher elevation), latitude (lower gravity closer to the equator), local geology and other factors.
Although gravity does not affect the mass of the weight on the scale, it does affect the force of the mass on the weighing instrument (Force = mass × acceleration due to gravity, g). And since a weighing instrument is measuring the force, the gravity affects the instrument’s reading. Local gravity differences may come into play if a weighing instrument is moved to a new location. In that case, it might need to be adjusted, depending on how accurate the instrument is and how much is it moved. Often, reference weights are calibrated in a different location than where they are used. Therefore, the gravity difference needs to be considered when use the reference weights to calibrate and adjust your weighing instruments.Air buoyancy. When weights are being used, air buoyancy results in a small force that reduces the force of the mass. So, in effect, air buoyancy lifts the weights up very slightly. The effect of air buoyancy depends on environmental conditions and on the differences of the density of the weights compared to air density. Because the effect of air buoyancy is relatively small, and does not change that much from day to day, it is not always considered.
Effect of convection. If the temperature of the weight differs from the environmental temperature, there will be an air convection around the weight. The wider the temperature differential, the larger the air convection will be. This convection will have a small effect on the indication of the weighing instrument.
For example, if the weight is colder than environment, the air convection around the weight will move downward facing the weighing instrument and cause small additional weight to the weighing instrument. The effect of convection is more relevant with high-accuracy instruments, although it is still relatively small.Substitution loads
Substitution loads are items that can be used for help in calibration if the available weights are insufficient for the calibration. An example is the case where the calibration of a 1,000-kg weigh scale is required, but only one weight of 100 kg and two weights of 200 kg (total 500 kg) are available. To address this, the procedure would be to calibrate the first points up to 500 kg using the weights you have, then read the exact indication of the weighing instrument with the 500-kg load. The weights would then be removed and a substitution load would be placed on the weighing instrument until the indication matches readout when the 500-kg weights were on the scale. When the substitution load has the same measured weight value as the available accurate reference weights, you can then continue by adding the existing reference weights to the load surface that is still holding the substitution load to reach the 1,000-kg target.Calibration certificate
An essential part of calibrations is to document the results with a calibration certificate. The certificate includes the measurement results of the calibration (that is, the mass of the weights placed on instrument and the indication of the instrument). The certificate should also include the total uncertainty of the calibration. Measurement values without related uncertainty do not tell very much about the measurement. The certificate should also include a clear description of the instrument being calibrated and the weights being used as reference. The calibration procedure that was followed should also be included. Environmental conditions during the calibration should also be included in the certificate. In summary, a calibration certificate should include the following information: • Measurement results • A unique certificate number • User company name, address and identification • Name, signature and company of the person who did the calibration • Detailed information on the instrument that was calibrated • Identification of the reference weights being used • Identification of the calibration procedure being used • Calibration date • Environmental conditions • Measurement uncertainty and its coverage factor • Mention of the case when only a partial calibration was done • A graphical representation of the calibration results if possible (useful visual component) If the calibration is accredited, then the regulation will stipulate the contents of the certificate.Uncertainty
In weighing instrument calibration, the uncertainty of the calibration should be known. Knowing the error of the scale indication at each calibration is not sufficient. Users must also know the uncertainty about the error found at each point of calibration. This section will discuss uncertainty at a more general level, rather than providing the details of how to carry out uncertainty calculations. Refs. 5 and 6 cover the uncertainty calculations in more detail.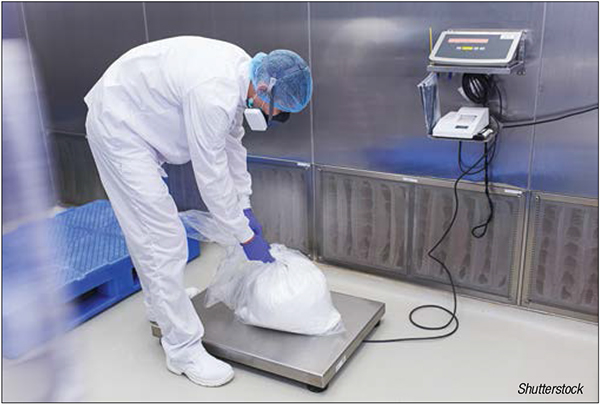
Edited by Scott Jenkins
References
1. EURAMET e.V. Technical Committee for Mass and Related Quantities, EURAMET Calibration Guide No. 18, Version 4.0, EURAMET e.V., Braunschweig, Germany, November 2015.
2. Butcher, T.G. and others, NIST Handbook 44 (2023 Edition) – Specifications, Tolerances, and Other Technical Requirements for Weighing and Measuring Devices, National Institute of Standards and Technology (NIST) Office of Weights and Measures, Gaithersburg, Md., 2022.
3. International Organization of Legal Metrology (OIML), OIML Standard R76-1, Non-automatic weighing instruments Part 1: Metrological and technical requirements – Tests, 2006 edition, OIML, Paris, France, , 2006.
4. BSI Group, EN 45501:2015, Metrological aspects of nonautomatic weighing instruments, British Standards Institution, 2015.
5. European Co-operation for Accreditation (EA), EA-4/02, rev. 3, Evaluation of the Uncertainty of Measurement in Calibration, EA, Paris, France, , April 2022.
6. International Bureau of Weights and Measures (BIPM), JCGM 100:2008, Evaluation of measurement data: Guide to the expression of uncertainty in measurement, BIPM, Paris, France, 2008.
Additional resources:
OIML, OIML R111: Weights of classes E1, E2, F1, F2, M1, M1-2, M2, M2-3 and M3, .
Council of the European Union, Directive 2009/23/EC,-Non-automatic weighing instruments, 2009.
Authors
Ned Espy, technical director, has been promoting calibration management with Beamex Inc. (2152 Northwest Parkway, Suite A, Marietta, Ga.; Email: [email protected]; Phone: 770-951-1927) for over 20 years. Espy has helped develop best practices for calibration, with a focus on pressure, temperature and multivariable instruments. He is a consistent editorial contributor to leading industry publications, and has received significant recognition within the automation industry. Today, Espy teaches calibration best practices and provides technical support to end users and the Beamex sales team.
Roy Tomalino has been teaching calibration management at Beamex (same address as above; Email: [email protected]) for over 20 years. He has taught on four different continents to people from over 40 countries. His previous roles include Technical Marketing Engineer and worldwide trainer for Hewlett Packard and Application Engineer with Honeywell. Today, Roy is a Beamex Calibration Evangelist. His primary mission is to demystify calibration and teach best practices.